Kim reformer
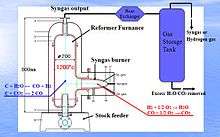
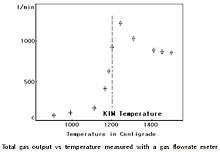
The Kim reformer is a type of syngas plant invented by Dr. Kim, Hyun Yong. It is a high temperature furnace (as shown in figure 1), filled with steam and/or carbon dioxide gas and maintaining a thermal equilibrium at a temperature just above 1200 °C, in which the reforming reaction is at its thermodynamic equilibrium and carbonaceous substance is reformed with the highest efficiency.
Dr. Kim, Hyun Yong discovered, in December 2000, that the reforming reaction (C + H2O ↔ CO + H2) proceeds at a temperature just above 1200 °C, but not below it. This work was published in International Journal[1] and registered in KR patent[2], US patent[3], CN patent[4] and JP patent[5].
Overview
The reformer reforms all carbon atoms of carbonaceous feedstock to produce just syngas, no other hydrocarbons. The high temperature furnace is packed with castables to minimize heat loss in such a way as to maintain the inner temperature of a reduction reactor filled with steam and carbon dioxide (CO2) gas at a temperature just above 1200 °C (aka Kim temperature, see figure 2),[1] and it reforms all carbonaceous substances most efficiently to produce syngas. The produced syngas exits from the reduction reactor at a temperature of 1200 °C. The reduction chamber is heated by super-hot gases (steam and CO2) generated in the syngas burner with oxygen gas. The reduction chamber must be constructed to withstand, physically and chemically, the reforming reaction at 1200 °C.
Advantages
Both steam reforming and dry reforming are carried out in this reformer; therefore, it is possible to configure the H2/CO ratio by adjusting the H2O/CO2 ratio in the reduction chamber. The reforming reaction is a very specific elementary reaction; all carbon atoms on the left are reformed into carbon monoxide and all hydrogen atoms are reduced to hydrogen gas. The mixture of two product gases is called syngas. These reforming reactions are an endothermic reduction reaction. In contrast, the conventional gasification reaction is a combination of several reactions operating below 1200 °C and the product is a mixture of many gases.
History of reforming reactions
The process for producing water gas (C + H2O → CO + H2) has been known since the 19th century and it was later found that it is applicable to all carbonaceous substances. Reactions C + H2O ↔ CO + H2 and (-CH2) + H2O → CO + 2H2 are called steam reforming and reactions C + CO2 → 2CO and (-CH2) + CO2 → 2CO + H2, carbon dioxide or dry reforming. The oil industry has used the reforming reactions extensively for the cracking process and to generate hydrogen gas.
References
- ↑ Kim Hyun Yong, Method of gasification in IGCC system, INT J HYDROGEN ENERG 32:5088-5093, 2007
Kim Reformer-XT
Kim reformer was constructed for the purpose of laboratory testing, and it is limited to an hourly capacity of 100m3 syngas production while Kim reformer-XT[6] has extended its hourly capacity to 500m3 syngas. A single -XT unit operating 20 hours a day can produce 2.5 tons of H2 gas per day. The Kim reformer-XT has a coke pile as primary heat source which maintains the reformer's temperature up to 1,000℃, and the secondary heat source of burning the recycling syngas to bring up the temperature of the upper half of the reforming furnace to 1,200℃ and maintain it so that the 500m3 syngas/hour output is achieved. This makes the Kim reformer-XT version very energy smart. The (-XT) version (Fig. 3) comprises gaseous carbonaceous feedstock input port(20); coke supply port(30, 31); oxygen gas input port(40, 42); steam input port(50); syngas output port(60). The coke is burned with oxygen and reacts with steam to generate a mixture of hot gases(CO2, H2O, CO, H2) and maintain the temperature of the entire furnace at about 1,000℃. Recycling syngas enters into the furnace at about the mid-level(70) and is burned with oxygen gas(42) placed just above(70). This burning syngas raises the temperature of the upper half of the reducing furnace to 1200℃ and higher, for an efficient reforming of all gaseous carbonaceous matter with no catalyst.